Know What You are buying
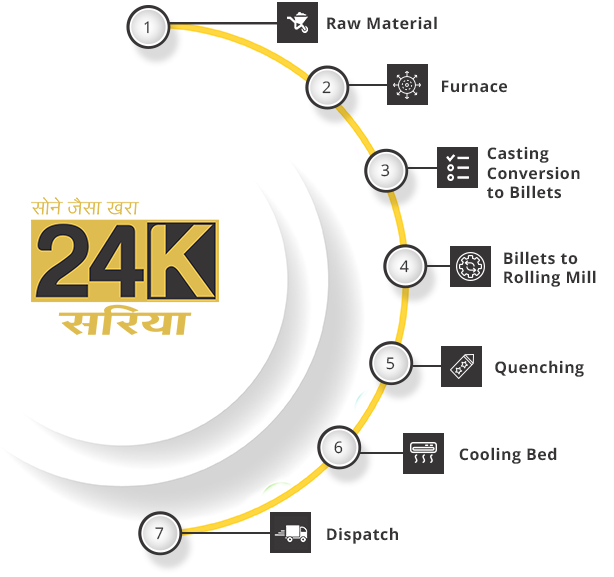
- 01Raw Material is bought and lab tested, Segregated as per properties and, selected or rejected.
- 02The selected raw material is put in a Furnace and converted to Molten metal at 1700° C. Ferrero alloys are added to maintain the composition to get desired quality and performance
- 03Molten metal is checked for composition and temperature and sent for casting. Billets are made, checked for quality and selected/rejected basis pre-approved parameters.
- 04The quality approved individual billets are sent to Rolling Mill where they are roughed and molded into TMT Bars of different sizes along with ribbing(X design)
- 05These rolled TMT Bars go for quenching in the patented Thermex cooling station where the Grades depicting strength of the Sariya(FE-500/FE-500D/FE-550) is achieved through fast cooling of the surface of the rods with fast jet of water.
- 06Our Sariya is ready and cut in pre-approved or desired length and sent on the cooling bed. Here both the tips
- 07Sariyas are ready for dispatch.
Manganese increases ductility and tensile strength of steel. It is able to decrease the critical cooling rate during hardening, thus ensuring softer core and harder outer surface. This increases ductility at same time increasing hardness of steel so to use in limited ratio.
Sulphur is detrimental to surface quality in low carbon and low manganese steel and it promotes hot shortness in welding with the tendency increasing with increased sulphur. It is regarded as an undesirable impurity because of its embrittling effect and hot shortness.
Phosphorus – It is regarded as an undesirable impurity because of its embrittling effect.
Copper is added to steel to increase corrosion resistance. It increases strength through precipitation hardening if present in concentrations greater than 0.075%.
Chromium Increases strength, hardness, and toughness, as well as creep resistance and strength at elevated temperatures. It improves machinability and resistance to corrosion and it intensifies the effects of other alloying elements. We maintain chromium at 0.12%.
Carbon – Adding carbon to iron makes it stronger and tougher, if added up to a point. Beyond that point it will get stronger but less tough (i.e.) like cast iron.